The global shift toward renewable energy and electric vehicles (EVs) has sparked unprecedented demand for lithium-ion batteries. However, with millions of batteries reaching end-of-life annually, recycling is no longer optional—it’s essential. For businesses exploring this sector, understanding the lithium ion battery recycling plant cost is critical.
Why Lithium-Ion Battery Recycling Matters
Lithium-ion batteries contain valuable metals like lithium, cobalt, and nickel. Recycling them reduces mining dependency, minimizes environmental hazards, and supports circular economies. Governments worldwide are enforcing stricter regulations, making battery recycling a lucrative—and necessary—venture. But before diving in, let’s demystify the costs.
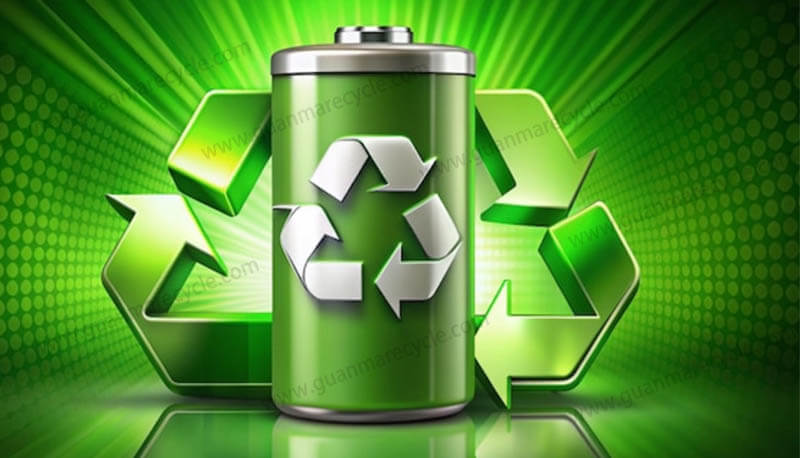
Breaking Down Lithium Ion Battery Recycling Plant Cost
Establishing a recycling facility involves multiple variables. Here’s a detailed cost analysis:
1. Initial Setup and Infrastructure Expenses
Land and Construction: Location significantly impacts land prices. Urban areas may offer logistical advantages but come with higher real estate costs. A medium-sized plant (capable of processing 10,000 tons annually) typically requires 5,000–10,000 sq. meters, costing $2–$5 million(This data is for reference only).
Equipment: Crushing machines, hydrometallurgical reactors, and sorting systems form the backbone of operations. Advanced systems like pyrolysis units or AI-driven sorting can raise equipment costs to $4–$8 million(This data is for reference only).
2. Technology and Process Selection
Mechanical vs. Chemical Recycling: Mechanical methods (shredding, sieving) are cheaper ($1–$3 million) but yield lower-purity materials. Hydrometallurgical or pyrometallurgical processes recover 95%+ of metals but require $6–$12 million in tech investments(This data is for reference only).
Automation: Integrating AI for waste sorting or robotic disassembly boosts efficiency but adds 15–20% to initial costs.
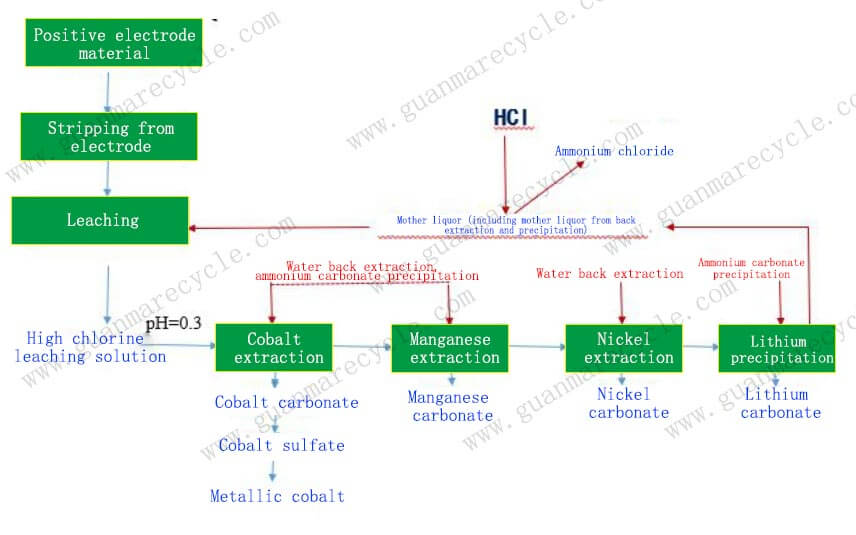
3. Compliance and Licensing
Meeting environmental and safety regulations is non-negotiable. Permits, waste disposal certifications, and emissions controls can add $500,000–$2 million, depending on regional policies (This data is for reference only).
4. Labor and Operational Costs
Skilled technicians, chemists, and engineers are vital. Annual labor costs range from $1–$3 million for a 50-person team(This data is for reference only).
Utilities (power, water) and maintenance account for 20–30% of ongoing expenses.
5. Feedstock and Logistics
Collecting spent batteries requires partnerships with OEMs, scrapyards, or municipalities. Transportation and storage costs vary widely—proximity to EV hubs or consumer electronics manufacturers can reduce logistics spend by 10–15%(This data is for reference only).
Key Factors Influencing Total Lithium Battery Recycling Plant Expenses
Scale: Small-scale plants (<5,000 tons/year) cost $8–$15 million, while large facilities (>20,000 tons/year) exceed $30 million.
Geography: Asia offers lower labor and construction costs; Europe and North America prioritize automation but face stricter regulations.
Material Recovery Rates: High-efficiency plants command higher setup costs but generate 40–60% more revenue from reclaimed metals.
Government Incentives: Tax breaks, grants, or subsidies can offset 10–25% of capital expenses.
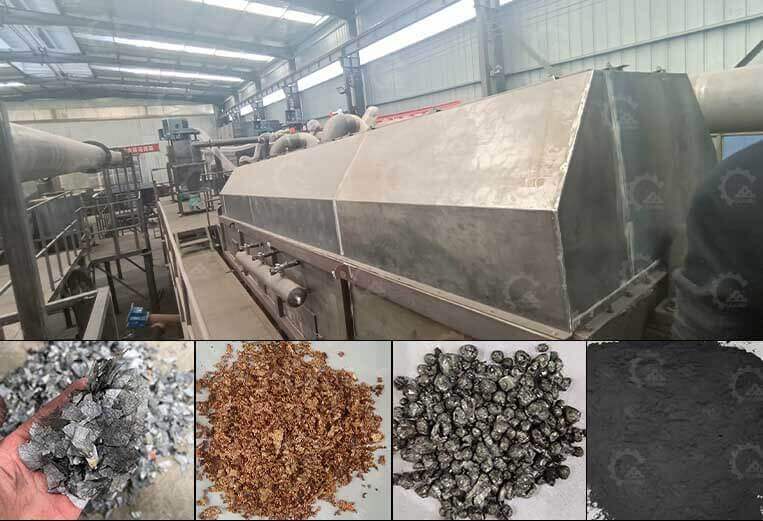
How to Reduce Lithium-Ion Recycling Plant Costs
1. Adopt Modular Designs: Phased expansions allow businesses to scale operations without overspending initially.
2. Leverage Partnerships: Collaborate with battery manufacturers for steady feedstock supply or co-locate with solar farms to cut energy bills.
3. Optimize Technology Mix: Combine mechanical pre-processing with targeted chemical recovery to balance purity and costs.
4. Explore Second-Life Applications: Resell functional batteries for grid storage before recycling, diversifying revenue streams.
Long-Term ROI of a Battery Recycling Plant
While startup costs are substantial, the long-term payoff is compelling:
Raw Material Savings: Recovered metals can slash procurement costs by 30–50%.
Carbon Credits: Eco-friendly operations qualify for tradable credits, adding $200–$500 per ton of recycled batteries(This data is for reference only).
Market Growth: The lithium-ion recycling market is projected to hit $23.7 billion by 2030, driven by EV adoption.
Is a Lithium-Ion Battery Recycling Plant Worth the Cost?
The lithium ion battery recycling plant cost is undeniably high, but so are the rewards. By analyzing location, technology, and scale, businesses can build a future-proof operation that aligns with global sustainability goals.