If your business deals with lead-acid batteries, investing in a lead acid battery recycling machine is not just an eco-friendly choice—it’s a strategic financial decision. However, selecting the right equipment requires careful evaluation.
Why Lead Acid Battery Recycling Machines Matter
Over 99% of lead-acid batteries are recyclable, making them one of the most sustainable energy storage solutions. However, improper recycling releases toxic lead and sulfuric acid, posing severe environmental and health risks. A dedicated lead acid battery recycling machine streamlines the process, ensuring:
Regulatory compliance: Meet strict international standards.
Resource recovery: Extract up to 98% of reusable lead and plastics.
Cost savings: Reduce waste disposal fees and generate revenue from recovered materials.
For businesses in the battery manufacturing, automotive, or waste management sectors, these machines are indispensable for long-term profitability and sustainability.
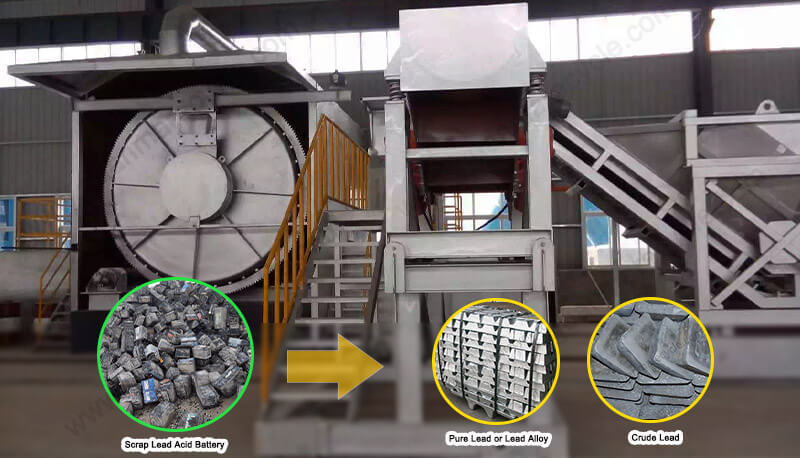
Key Factors to Consider Before Buying
1. Processing Capacity & Efficiency
The machine’s capacity must align with your operational needs. Ask:
What’s your daily/monthly battery volume? Small-scale operations may opt for 1–5 ton/day systems, while industrial recyclers need 20+ ton/day machines.
What’s the recovery rate? High-end systems achieve 95–98% material recovery.
Is it automated? Automated sorting, crushing, and separation reduce labor costs and human error.
2. Technology & Safety Features
Advanced recycling machines prioritize safety and efficiency:
Closed-loop systems: Prevent lead dust and acid leakage.
Anti-explosion designs: Critical for handling sulfuric acid and gases.
Emission controls: Scrubbers and filters to meet air quality standards.
Avoid outdated “open furnace” systems, which are inefficient and pose significant safety hazards.
3. Certifications & Compliance
Ensure the machine complies with:
ISO certifications (e.g., ISO 9001, 14001): Indicates quality and environmental management.
Regional regulations: For example, EU’s BAT (Best Available Techniques) or OSHA standards in the U.S.
CE/RoHS markings: Essential for exporting to European markets.
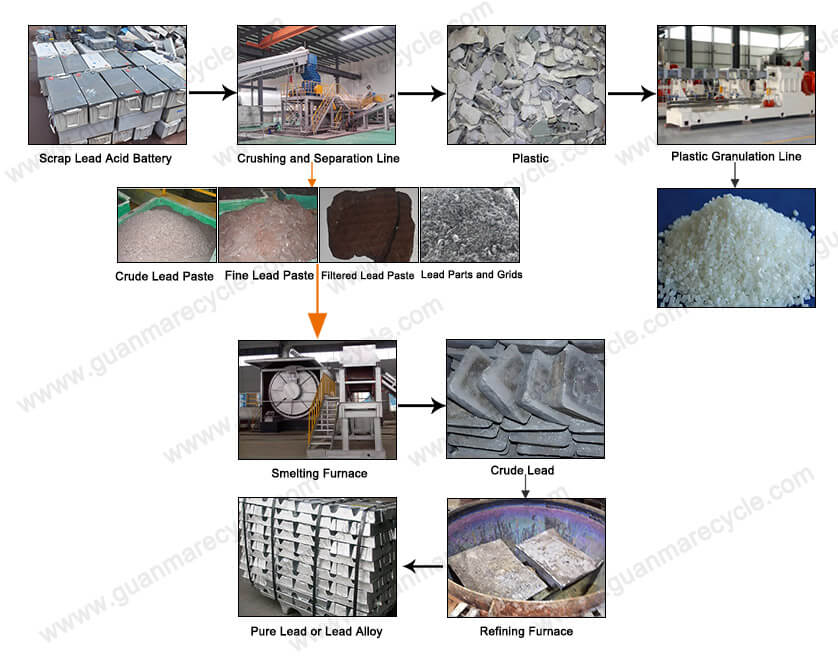
4. After-Sales Support & Maintenance
Recycling machines require regular maintenance. Prioritize suppliers offering:
On-site training: Proper operation minimizes downtime.
Spare parts availability: Check lead times for critical components like crushers or filters.
Warranty: Look for at least 1–2 years of coverage.
5. Total Cost of Ownership (TCO)
While upfront costs matter, calculate long-term expenses:
Energy consumption: High-efficiency systems reduce power bills.
Labor costs: Automated machines cut workforce requirements.
How to Choose a Reliable Lead Acid Battery Recycling Machine Supplier
Not all recycling machine manufacturers are equal. Follow these steps to vet suppliers:
1. Request case studies: Ask for client testimonials or project examples in your region.
2. Test the equipment: Reputable suppliers offer live demos or factory inspections.
3. Compare quotes: Balance cost with technology, certifications, and after-sales service.
Top Applications of Lead Acid Battery Recycling Machines
These systems are vital across industries:
Battery manufacturers: Recycle production scrap and defective units.
Auto repair shops: Dispose of used car batteries safely.
E-waste recyclers: Process UPS, telecom, and industrial batteries.
Government agencies: Support municipal recycling programs.
Investing in a lead acid battery recycling machine is a smart move for businesses aiming to reduce environmental impact while unlocking new revenue streams.