As global demand for electric vehicles (EVs) and renewable energy storage surges, lithium-ion battery recycling has emerged as a critical—and profitable—industry. However, understanding the cost of setting up a lithium-ion battery recycling plant is essential to avoid financial pitfalls and maximize long-term returns.
Why Invest in a Lithium-Ion Battery Recycling Plant?
Before diving into costs, let’s address the why. By 2030, over 11 million metric tons of lithium-ion batteries will reach end-of-life annually. Recycling these batteries:
Recovers valuable metals (lithium, cobalt, nickel) worth $30–$50 per kWh of battery capacity.
Reduces reliance on mining, lowering carbon emissions by up to 70%.
Complies with tightening regulations (e.g., EU Battery Directive, U.S. Inflation Reduction Act incentives).
But to capitalize on this opportunity, you need a clear breakdown of the investment for lithium-ion recycling facility setup.
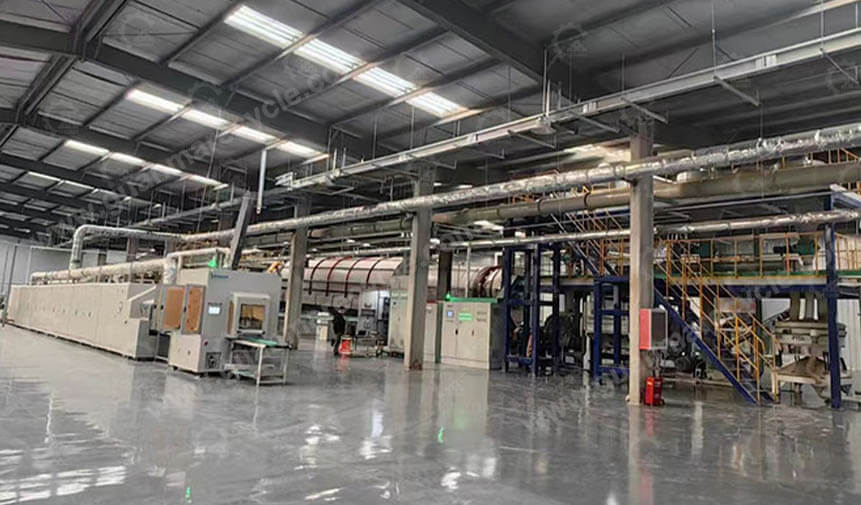
Breaking Down the Cost of Setting Up a Lithium-Ion Battery Recycling Plant
1. Pre-Treatment and Sorting Equipment
The first step involves safely discharging and dismantling batteries. Key machinery costs include:
Battery Shredders: $150,000–$500,000 (depending on capacity).
Sorting Systems (e.g., magnetic separators, air classifiers): $200,000–$800,000(depending on capacity).
Safety Infrastructure: Explosion-proof rooms and gas detection systems add $100,000–$300,000(depending on capacity).
Total: $450,000–$1.6 million.
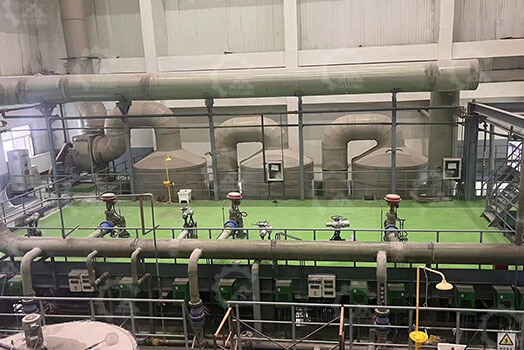
2. Hydrometallurgical or Pyrometallurgical Processing
This stage extracts metals from battery “black mass.” Costs vary by technology:
Pyrometallurgy (high-temperature smelting):
Furnaces and emission control systems: $2–$5 million(Costs vary by technology).
Higher energy costs ($500–$1,000 per ton processed)(Costs vary by technology).
Hydrometallurgy (chemical leaching):
Reactors, solvent extraction units: $1–$3 million(Costs vary by technology).
Total: $1–$5 million(Costs vary by technology).
3. Refining and Purification
To produce battery-grade metals, you’ll need:
Electrowinning Systems: $500,000–$2 million(Costs vary by technology).
Crystallization Equipment: $300,000–$1 million(Costs vary by technology).
Quality Control Labs: $200,000–$500,000(Costs vary by technology).
Total: $1–$3.5 million(Costs vary by technology).
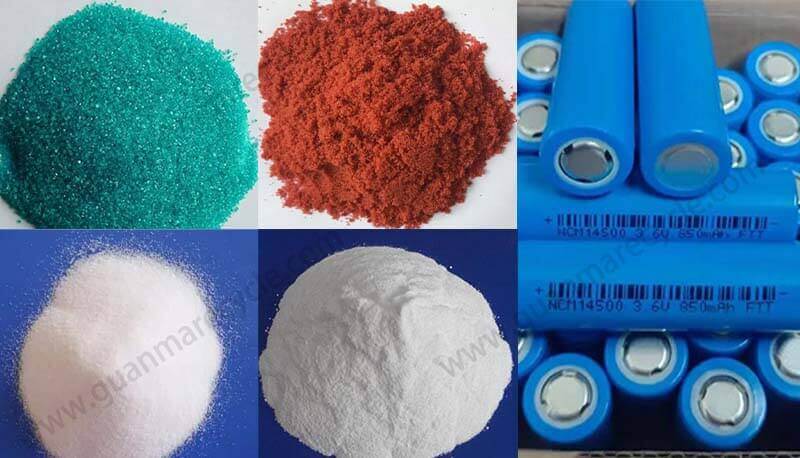
4. Facility and Permits
Land and Construction: A 10,000–20,000 sq. ft. facility costs $1–$3 million in regions like India or Southeast Asia. In the EU or U.S., this rises to $4–$8 million(The actual data shall prevail and this data is for reference only).
Permits and Compliance: Environmental licenses, fire safety approvals, and hazardous waste permits add $100,000–$500,000(The actual data shall prevail and this data is for reference only).
Total: $1.1–$8.5 million(The actual data shall prevail and this data is for reference only).
5 Strategies to Reduce Lithium-Ion Battery Recycling Plant Setup Costs
1. Opt for Modular Systems
Start with pre-assembled, scalable units to avoid overinvesting upfront.
2. Target Government Grants
Countries like Canada and Germany offer subsidies covering 30–50% of recycling equipment costs.
3. Partner with OEMs
Collaborate with EV manufacturers for guaranteed feedstock supply and shared R&D costs.
5. Focus on High-Value Metals
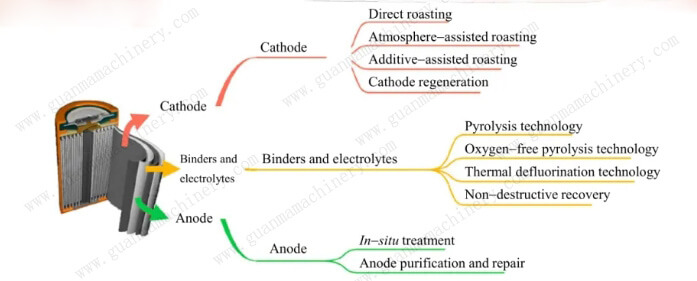
Is a Lithium-Ion Battery Recycling Plant Worth the Investment?
The cost of setting up a lithium-ion battery recycling plant is significant, but the long-term rewards are compelling. With metal prices rising and global recycling rates below 5%, early movers can dominate this $30+ billion market.
Ready to launch your project? Contact us today for a customized cost analysis, equipment recommendations, and financing solutions tailored to your lithium-ion battery recycling plant budget.